두 차례 공장 스마트 화 진행한 작소기업 삼창선재
"중국산 저가 제품 상대하기 위해 도입 결정"
"도입 후 현장 직원 위험과 번거로움 많이 줄어"
"생산성·에너지 효율↑...데이터 다루는 직원도 채용"
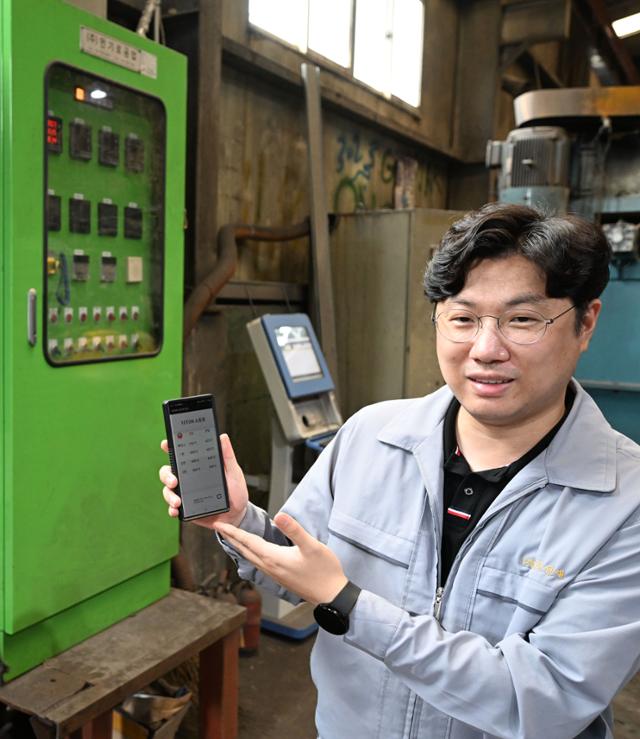
박민기 ㈜삼창선재 대표가 공장 핵심 설비인 전기로에 도입한 인터페이스를 설명하고 있다. 배우한 기자
"매일 오후 11시마다 전기로(爐) 전원을 직접 켜기 위해 직원이 출근해야 했는데, 스마트 공장을 도입한 뒤론 이 작업이 사라졌어요. 기계가 정해진 시간에 알아서 돌아가기 때문에 더 이상 어두컴컴한 밤에 졸린 눈을 부비며 위험한 설비가 가득한 공장에 들어가 전원 버튼을 켜지 않아도 되죠."
지난달 27일 스마트 공장 도입 후 달라진 점을 설명하는 박민기(39) ㈜삼창선재 대표의 입가에 미소가 번졌다. 박 대표는 "무엇보다 우리 공장의 핵심이라 할 수 있는 전기로 온도를 담당 직원의 '감(感)'에 의존하지 않고 데이터에 따라 체계적으로 운영할 수 있게 됐다"고 말했다.
직원 17명인 소기업이 스마트 공장 도입
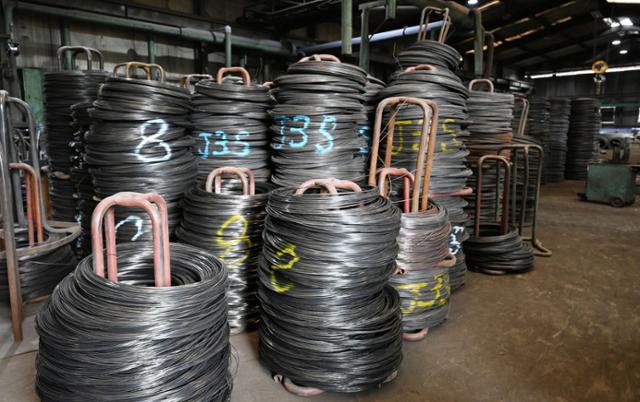
지난달 27일 경기 양주에 위치한 ㈜삼창선재 공장 내부에 열처리를 마친 철선들이 빼곡하게 쌓여 있다. 배우한 기자
삼창선재는 건설자재 중 하나인 철강선을 제조하는 업체다. 연매출 95억 원에 직원 20인 미만의 중소기업이 스마트 공장을 도입한 데는 박 대표의 절박함이 컸다. 중국산 저가 제품이 물밀 듯 들어와 국내 시장을 빠르게 점유하면서 '이러다 다 죽겠다' 싶었던 것. 품질을 떨어뜨리지 않으면서 가격 경쟁력을 가지려면 사람에 대한 의존을 줄이고 시스템화해야겠다는 생각이 들었다. 그는 "솔직히 처음엔 스마트 공장이 뭔지 잘 모르는 채로 무턱대고 신청했는데 첫 성과가 나쁘지 않았다"고 말했다.
직원 부상 위험 줄이고 생산량 데이터화 성공
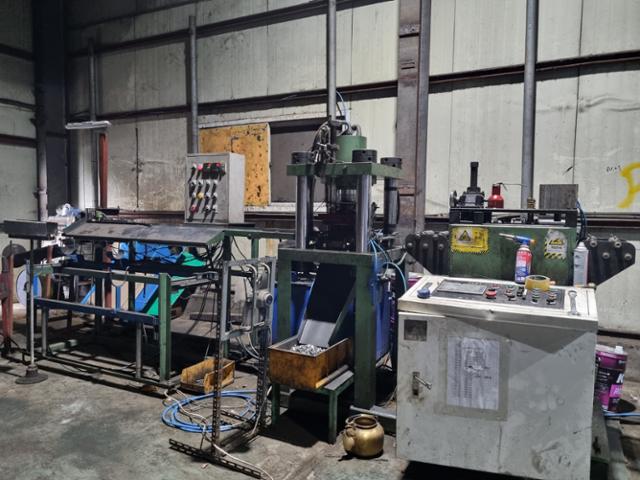
1차 스마트 공장 도입 당시 구축한 유압 프레스기. 전원을 켜면 기계가 자동으로 작동되면서 핀을 찍어 낸 뒤 개수를 세어 컴퓨터로 전송한다. 김진주 기자
박 대표는 두 번에 걸쳐 스마트 공장을 도입했다. 첫 번째 시도는 2018년이다. 콘크리트 거푸집 고정용 핀을 제작하는 프레스를 유압 프레스로 바꾸면서 데이터 생성 및 전송, 기록 등을 위한 인터페이스를 구축했다. 기존 프레스는 직원들이 손수 기계에 판을 넣고 찍어 내야 했기 때문에 부상이 잦았다. 프레스 숙련공치고 손가락이 멀쩡한 사람이 없을 정도다. 이 공장에 처음 온 프레스 담당 직원도 이미 손가락 2개가 없었다. 게다가 결과물을 일일이 세는 번거로움도 상당했다.
스마트 공장을 도입한 뒤론 이 같은 위험과 번거로움이 사라졌다. 유압 프레스가 알아서 핀을 찍어 낸 뒤 개수를 세어 컴퓨터로 전송해주기 때문이다. 몇 개가 생산됐는지 바로바로 확인이 가능해 생산량을 조절할 수 있음은 물론, 재고량 파악도 손쉬워졌다.
2020년 2차 시도 땐 핵심 설비 스마트화
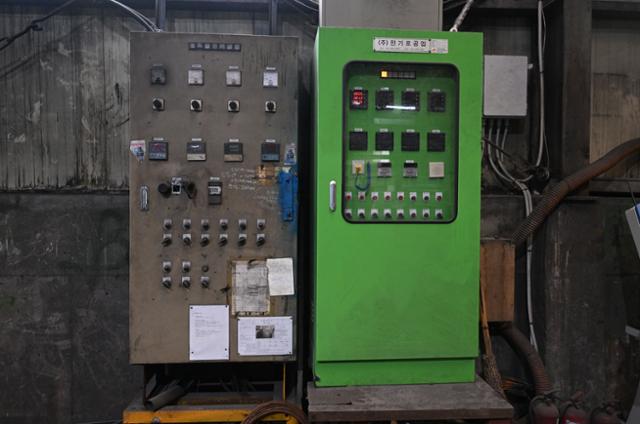
2차 스마트 공장 도입 때 구축한 전기로 조작장치. 왼쪽이 구형, 오른쪽이 신형이다. 구형은 사람이 일일이 손으로 조작해야 하지만 인터페이스가 구축된 신형은 언제 어디서든 PC나 휴대폰으로 조작 가능하다. 배우한 기자
한 번 해보니 자신감이 붙었다. 지난해엔 중소벤처기업부, 중소기업중앙회, 포스코와 함께 상생형 스마트공장에 도전했다. 상생형 스마트공장은 대기업이 중소·중견기업과 협력해 스마트공장을 구축하면 정부가 구축비용의 일부를 지원하는 것으로, 대·중소기업 동반성장을 겨냥하고 있다. 이번엔 핵심 설비 중 하나인 전자로 부분에 디지털 인터페이스를 도입했다. 박 대표는 "10년 묵은 체증이 내려갔다"고 했다. 그도 그럴 것이 전기로 온도에 따라 철선의 강도가 달라지는데, 전기로 온도는 외부 온도의 영향을 받기 때문에 섬세한 조정이 필요했다.
하지만 이 모든 것을 사람이 일일이 손으로 조작하고 기록하다 보니 정작 필요한 때 정확한 정보를 찾기가 어려웠다. 요즘같이 기온이 들쑥날쑥한 때는 사실상 담당자의 '감(感)'에 맡기는 수밖에 없다. 박 대표는 "한 번에 제대로 열처리를 하지 못해 재가열한 적도 있고, 아예 다 타 버린 적도 있다"며 "버리면 한순간에 1,500만 원이 날아간다"고 말했다. 재가열 또한 만만찮은 전기료가 든다.
생산성·에너지 효율 '쑤욱'
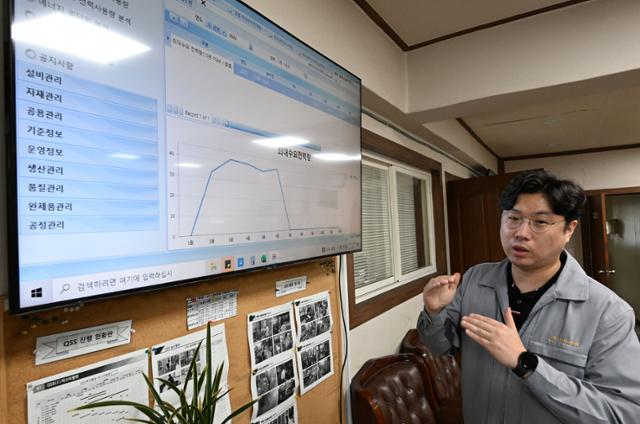
스마트 공장 도입 후 ㈜삼창선재는 에너지 효율과 생산성 모두 향상됐다. 박 대표 왼쪽에 달린 텔레비전에서 실시간으로 관련 데이터를 확인할 수 있다. 배우한 기자
설비를 바꾸고, 인터페이스를 도입하면서 환경은 180도 달라졌다. 설비를 PC나 휴대폰으로 제어할 수 있어 전기로에 이상이 생기면 재빠르게 시정할 수 있다. 뿐만 아니라 바깥 온도와 습도에 따른 전기로 온도와 철선의 강도가 자동으로 기록돼 언제든 필요한 정보를 찾아낼 수 있다.
덕분에 생산성은 2.5배 향상됐고, 에너지 효율이 좋아져 전기료가 kg당 10원 정도 줄었다. 한 달에 600톤~700톤 가량을 생산하니 월 600만 원 정도를 절약하는 셈이다. 요즘 같은 전기료 부담이 커지는 시기에는 엄청난 이점이다. 고용도 늘었다. 디지털 인터페이스가 구축되면서 데이터를 다룰 줄 아는 관리자급 직원을 한 명 채용했다. 박 대표는 "기계가 자동화되면 고용이 줄 것 같지만 그렇지 않다"며 "사람이 직접 생산에 관여하는 대신 생산을 관리하는 방향으로 가고 있는 만큼 이에 해당하는 인력 수요가 늘어날 것"이라고 말했다.
"빠른 확산 위해선 6070 대표들 설득이 관건"
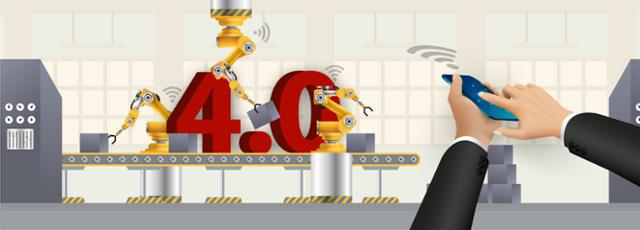
게티이미지뱅크
하지만 스마트 공장의 혜택을 모두가 누리는 건 아니다. 박 대표가 속한 철선공업협동조합의 50개 회원사 중 스마트 공장을 도입한 곳은 3, 4곳 뿐이다. 모두 40, 50대 젊은 대표가 있는 곳이다. 대부분은 대표 나이가 60, 70대라 컴퓨터 조작이 필요한 새 시스템 도입을 꺼린다. 이들에겐 스마트 공장 도입을 신청하기 위한 서류 작업도 쉽지 않다. 이미 수십 년 동안 몸으로 하는 노동에 익숙해진 고령의 직원들 또한 새 시스템을 반기기보다 위협적으로 받아들이는 경우가 많다. 자신의 일자리를 빼앗길까 두려운 것이다.
이뿐만이 아니다. 30년 이상 된 구형의 수동 장비로는 스마트 공장을 구축할 수 없어 설비 교체가 필수인데, 이 비용이 만만치 않다. 정부 지원금은 대부분 소프트웨어 구축에 들어가기 때문에 설비 교체 비용은 기업이 마련해야 한다. 박 대표 또한 1·2차 통틀어 설비 교체에만 2억 원 이상의 적지 않은 비용을 투자했다.
박 대표는 "스마트 공장을 하면 좋다는 걸 다 알면서도 비용 등 측면을 고려하다 보면 쉽게 결정하기 어려운 측면이 있다"며 "중국 저가 제품과 원자재가 상승 등으로 흔들리는 뿌리산업이 스마트 공장 도입을 통해 탄탄한 기반을 다질 수 있도록 정부가 보다 섬세하게 살펴줬으면 좋겠다"고 말했다.
기사 URL이 복사되었습니다.
댓글0