효율 극대화한 적기 생산 방식 위험성 노출
공급망 위기에 대비한 비축·자체 생산 고심
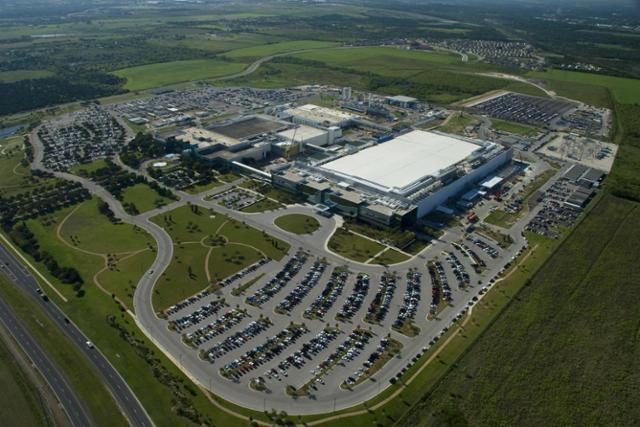
미국 텍사스주의 기록적인 한파로 가동이 중단됐던 삼성전자 오스틴 반도체 공장. 삼성전자 제공
‘효율성’은 현재의 이익을 보장하지만 불확실한 미래를 책임져 주진 않는다. 최근 ‘반도체 대란’을 겪으며 글로벌 자동차 업계가 뼈저리게 깨달은 교훈이다. 수요가 넘쳐나는데도 부품이 없어 자동차를 못 만들 거라고는 추호도 예상하지 못했다. 글로벌 공급망에 닥친 위기는 이제 생산 방식까지 바꾸고 있다. 주문 즉시 부품을 공급받아 완성품을 만드는 ‘저스트 인 타임(Just in Time)’, 이른바 ‘적기 생산’ 시스템을 재고하고 공급 불안정성에 대비한 보완책을 마련해야 한다는 것이다.
3일(현지시간) 미국 일간 월스트리트저널에 따르면 자동차 회사들은 반세기 동안 업계의 금과옥조로 여겨졌던 적기 생산 방식에서 벗어나 핵심 부품을 창고에 비축하기 시작했다. 심지어 적기 생산 방식을 개발해 표준화시킨 일본 도요타조차 일부 부품을 4개월치 이상 확보해 뒀다고 한다. 재고 관리 비용을 아껴서 얻는 이득보다 돌발 위기로 발생하는 손실이 더 크다는 판단에 따른 것이다. 덕분에 반도체 위기 상황에서 경쟁사들보다 피해가 적었다. 아슈와니 굽타 닛산 최고운영책임자(COO)는 “적기 생산 방식은 공급망 효율성 제고와 규모의 경제를 위해 설계됐다”며 “신종 코로나바이러스 감염증(코로나19)처럼 예상치 못한 위기에 취약성을 드러냈다”고 지적했다.
코로나19 외에도 갑작스러운 기상이변과 최근 수에즈운하 봉쇄 사태처럼 글로벌 공급망을 뒤흔드는 악재는 많다. 2월 미 텍사스주(州)를 강타한 이례적인 눈폭풍으로 전기 공급이 끊기면서 오스틴에 있는 삼성전자 반도체공장이 가동을 멈췄다. 미국 내 생산량 85%를 차지하는 합성수지 공급도 텍사스 정유공장들이 문을 닫으면서 막대한 차질이 빚어졌다. 반도체 물량 부족만으로도 버거운데 범퍼, 운전대, 시트 등에 들어가는 합성수지까지 동이 나 자동차 업계의 어려움은 가중됐다. 전 세계 해상 물동량 12%를 차지하는 수에즈운하가 초대형 컨테이너선 좌초로 가로막혔던 고작 일주일 동안에도 전 세계가 71조원에 달하는 ‘물류 대란’을 겪었다.
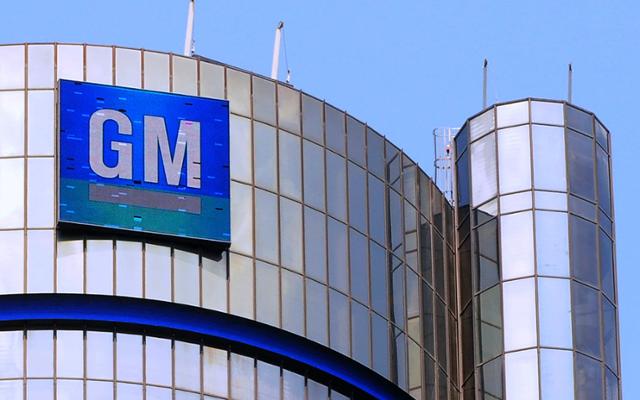
미국 디트로이트에 위치한 제너럴모터스(GM) 본사 전경.
자동차 업계의 전기자동차 전환도 부품 비축 필요성과 물량 확보 경쟁을 부추긴다. 반도체뿐 아니라 배터리 등 첨단 부품이 훨씬 많이 필요하기 때문이다. 더구나 이런 부품들은 여러 회사들이 단일한 공급체를 이용하기 때문에 위기 상황이 닥치면 업계 전체가 연쇄 피해를 보게 된다. 자동차 회사들이 자체적으로 핵심 부품 생산을 시작한 이유다. 제너럴모터스(GM)는 LG에너지솔루션과 오하이오에 23억달러(약 2조6,000억원) 규모 배터리 공장을 짓고 있다. 폭스바겐도 배터리 공장 6곳을 건설하고 2030년까지 140억달러(15조8,000억원)를 추가 투입하기로 했다. 나아가 테슬라는 배터리에 들어가는 핵심 소재까지 자체 조달할 계획을 세웠다. 지난해 9월엔 노스캐롤라이나주 리튬 광산과 계약을 맺었다.
짐 팔리 포드 최고경영자(CEO)는 최근 한 포럼에서 “다른 대다수 산업 분야에선 반도체 같은 핵심 부품을 안전하게 쌓아 놓고 사용한다”며 “수요보다 수년 앞서 비용을 선불로 지급한다”고 말했다. 그는 “자동차 공급 기반에 대해 올해 새롭게 알게 된 사실들은 매우 충격적이었다”며 “더 많은 재고를 비축해 두는 방안을 고려해야 한다”고 조언했다.
기사 URL이 복사되었습니다.
댓글0