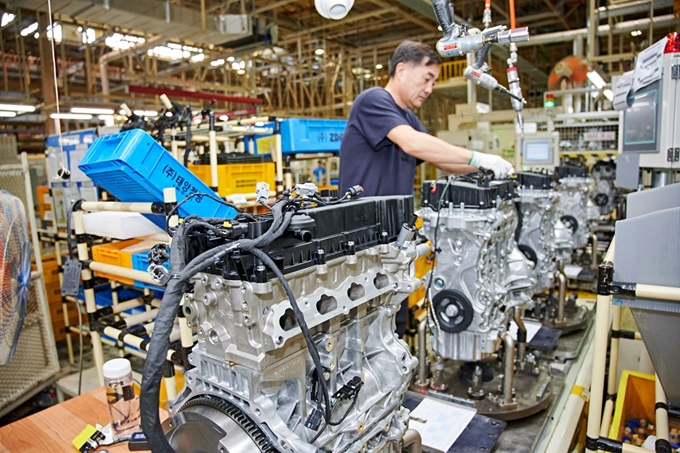
“창원공장의 시작은 메르세데스-벤츠와 함께한 ‘혈통’이라고 볼 수 있다. 1991년 기술제휴를 통해 설계 기술과 생산 시스템을 가져왔다. 최근 양산을 시작한 신형 1.5 직분사 가솔린(GDI) 터보 엔진은 벤츠의 품질 정책을 따른 명품엔진이다. 불량률은 100만대 당 50대꼴로 사실상 ‘제로’에 가깝다“
민병두 쌍용자동차 창원공장 담당 상무는 차세대 엔진인 1.5 GDI 엔진을 이렇게 설명했다. 37개월의 개발 기간을 거친 1.5 GDI 터보 엔진은 쌍용차의 소형 스포츠유틸리티차량(SUV) ‘티볼리’와 준중형 SUV ‘코란도’에 장착된다. 최근 ‘가솔린 SUV’에 대한 수요가 높아지면서 1.5 GDI 엔진은 올해 하반기 쌍용차 도약을 이끌 ‘새 심장’으로 평가받고 있다.
18일 방문한 경남 창원시 성산수의 쌍용차 엔진공장. 이 공장은 하나의 라인에서 디젤, 가솔린 엔진을 동시에 만들 수 있는 ‘혼류생산’ 시스템을 구축했다. 많은 기종을 생산해야 하는 쌍용차 라인업에 맞춘 생산 방식이다. 그 시작점에는 독일 프리미엄 브랜드 ‘벤츠’가 있다. 쌍용차와 벤츠는 1991년 디젤 엔진, 1992년 가솔린 엔진 기술 제휴를 맺었다. 벤츠의 생산ㆍ품질 시스템과 철학을 이어받은 이 공장은 불량률이 현저히 낮다.
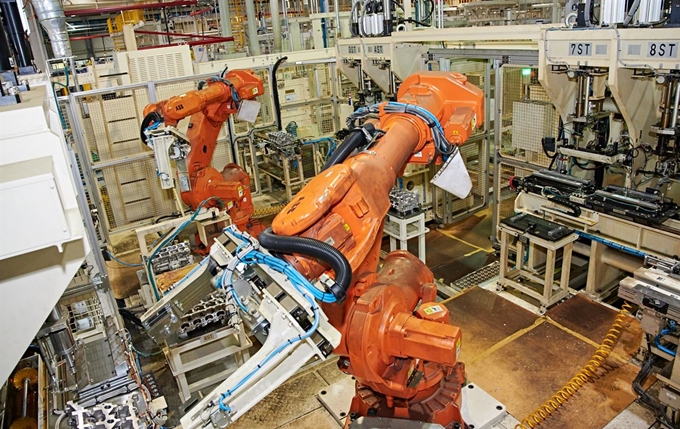
창원공장 생산라인은 바쁘게 돌아갔다. 가솔린 SUV 인기가 높아지면서 1.5 GDI 터보 엔진 생산물량이 크게 늘었기 때문이다. 특히 코란도의 경우 가솔린 모델 비중이 58%까지 확대됐다. 자동화율이 100%에 가까운 가공라인은 밀링머신, 로봇이 엔진 부품을 만들고 있었다. 특히 실린더헤드 등을 가공하는 라인은 사람 손길을 하나도 거치지 않았다.
변진수 쌍용차 생산기술팀 팀장은 “실린더 헤드 생산라인은 자동화율이 100%로, 20개 공정을 모두 로봇과 기계가 담당하고 있다”면서 “냉각수 등 유해물질이 ‘토크백’ 시스템을 통해 외부에서 처리되는 등 환경부 규제를 충족하는 친환경 공장”이라고 말했다.
가공을 마친 엔진 부품은 ‘무인 운반차(AGV)’에 실려 조립라인으로 옮겨졌다. 사람이 거의 없는 가공라인과 달리 조립라인은 수십 명의 사람들이 눈코 뜰 새 없이 기계를 조작하고, 엔진을 조립했다. 모든 공정을 거쳐 하나의 엔진이 생산되는 데 소요되는 시간은 5시간. 시간당 최대 25개의 엔진을 생산하는 1공장은 하루 평균 338개의 엔진을 만든다.
생산된 엔진은 총 12단계의 품질검증평가 시스템을 거친다. 쌍용차는 전산을 통해 품질정보를 관리하고 문제 발생 시 즉시 확인할 수 있도록 하는 ‘RFID(무선주파인식) 시스템’을 도입해 품질을 관리한다. 검증평가를 마친 엔진은 화물차 한 대에 87개씩 실려 평택공장으로 운송된다.
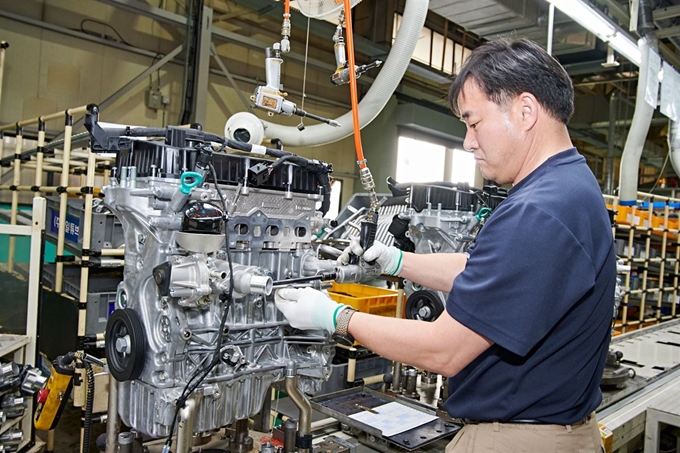
창원공장은 설립 이후 누적 생산량 290만대를 기록 중이다. 엔진에 필요한 부품 1,126개 중 1,069개를 국내 업체로부터 조달받고 있어 부품 국산화율이 95%에 달한다.
창원=류종은 기자 rje312@hankookilbo.com
기사 URL이 복사되었습니다.
댓글0